MAKING OF CAPE
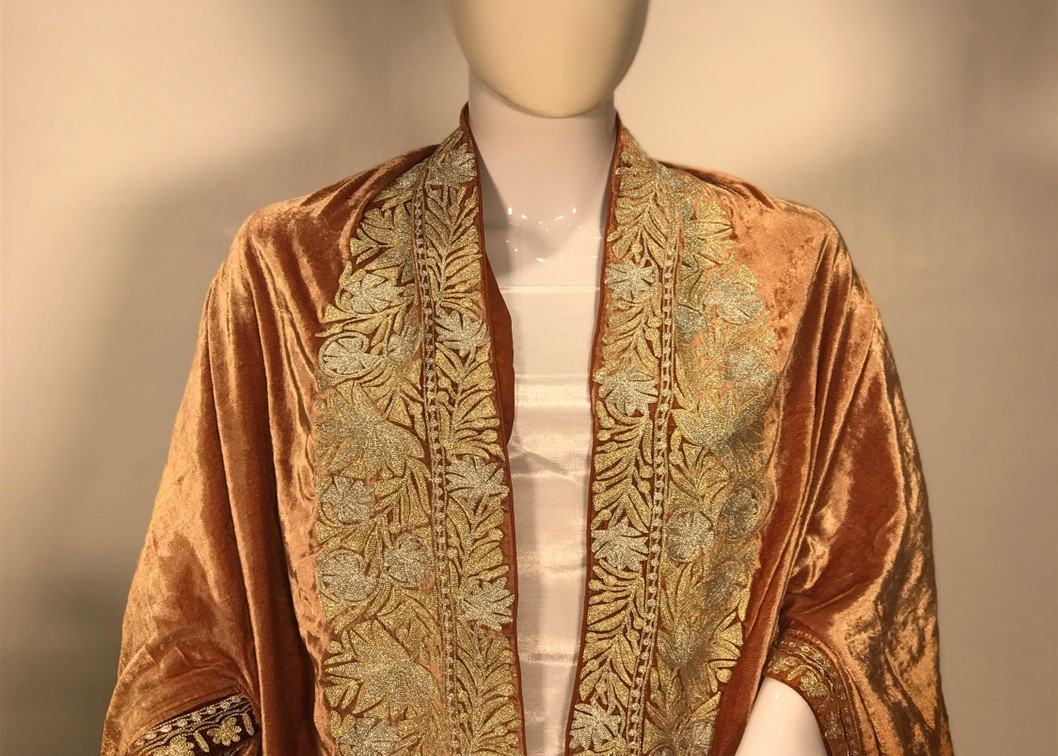
The manufacturing of Kashmiri capes, like many traditional garments, has roots in the cultural heritage of the Kashmir region. While it’s challenging to pinpoint an exact date for when the manufacturing of Kashmiri capes started. Kashmir has a rich tradition of textile production dating back centuries. The region is renowned for its skilled artisans who produce exquisite handcrafted textiles including shawls, scarves and capes. Kashmiri textiles gained prominence during the Mughal period in India (16th to 19th centuries), when they were highly prized for their quality and beauty. Mughal emperors and nobility were patrons of Kashmiri artisans, commissioning elaborate shawls and garments for their courts.
PRODUCTION OF KASHMIRI CAPES
Each step in the manufacturing process requires skilled labor, quality materials and adherence to industry standards to produce high-quality women’s capes efficiently:
- Designing and pattern making
- Fabric selection and cutting
- Assembly
- Adding closure
- Hemming
- Pressing and finishing
- Try on and adjust
- Optional Embellishment
MAKING OF CAP
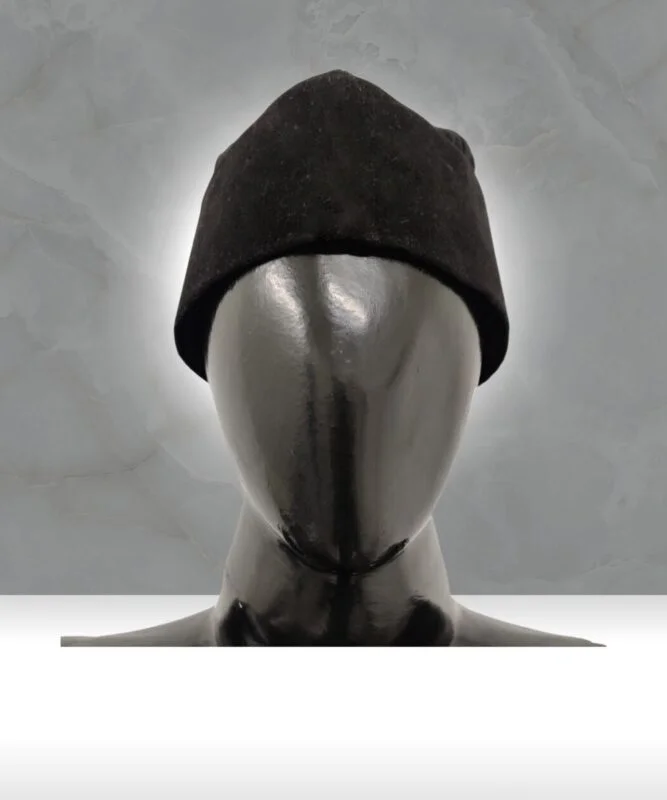
The Kashmiri cap holds symbolic significance as a marker of Kashmiri identity and cultural pride. It is not just a piece of clothing but a symbol of heritage and tradition for the people of Kashmir. In more recent times, the Kashmiri cap has also taken on political symbolism. The cap has become a recognizable symbol of Kashmiri resistance and solidarity. The elegance and craftsmanship of the Kashmiri cap have garnered international recognition, with people from around the world appreciating its beauty and cultural significance. It has also inspired fashion designers and enthusiasts to incorporate elements of Kashmiri embroidery and design into contemporary clothing styles. Al-Basir has taken an initiate to produce a wide range of Himachali caps along with Kashmiri caps also.
PROCESS OF MAKING CAP
The making of a Kashmiri cap involves intricate craftsmanship and attention to detail. While the exact process may vary depending on the style and design of the cap, here is a general procedure for making a traditional Kashmiri cap:
- Selection of material
- Design and pattern
- Fabric preparation
- Embroidery
- Finishing
- Final touches
- Assembly
- Quality check
- Packaging
MAKING OF SCARF
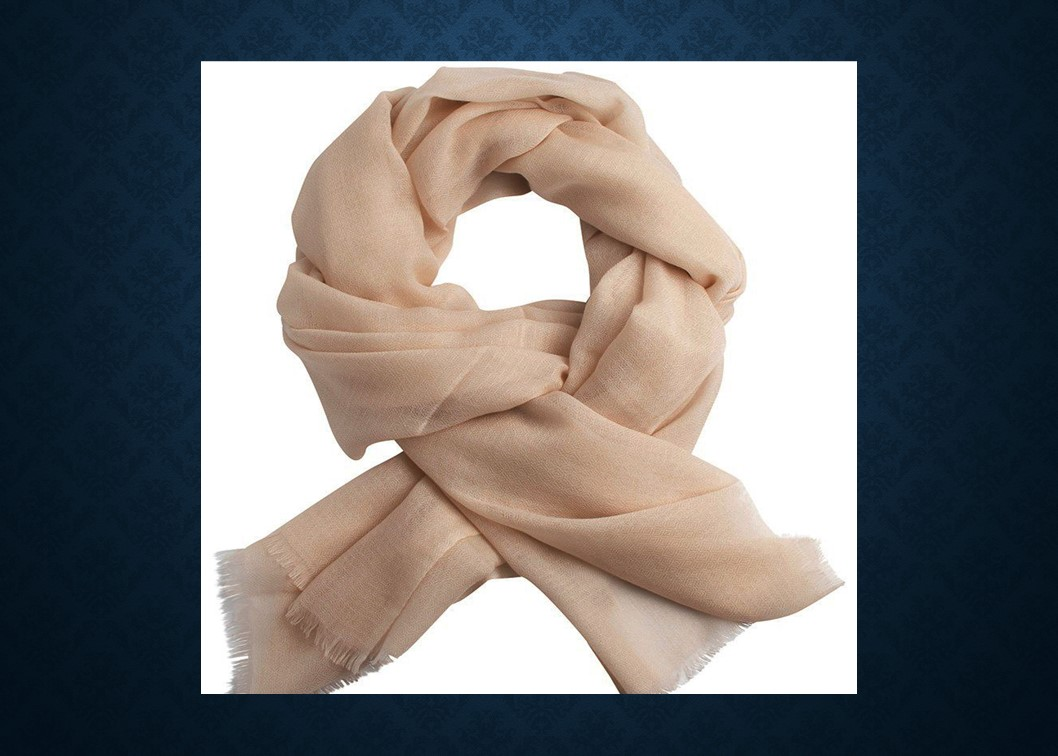
Kashmiri scarves are converted fabrics that have a rich history of being the most valued possession. Pashmina scarves come from Cashmere which is often referred to as soft gold, owing to its heavenly softness, lightweight texture and fine weave. The weaving of Cashmere to produce fine Kashmiri Pashmina scarves dates back to 3000 BC in Kashmir. Back then, it was just the affluent population that could afford and hence wear Pashmina scarves. The royal courts, hence, enjoyed the luxury of this coverted fabric in their courts.
MAKING PROCESS OF SCARF
The making of Pashmina scarves in Kashmir is a complicated process. Here is an overview of all the processes that go into the making of one shawl:
- Spinning
- Weaving
- Finishing
- Washing
- Dyeing
- Stretching
MAKING OF POTLI BAG
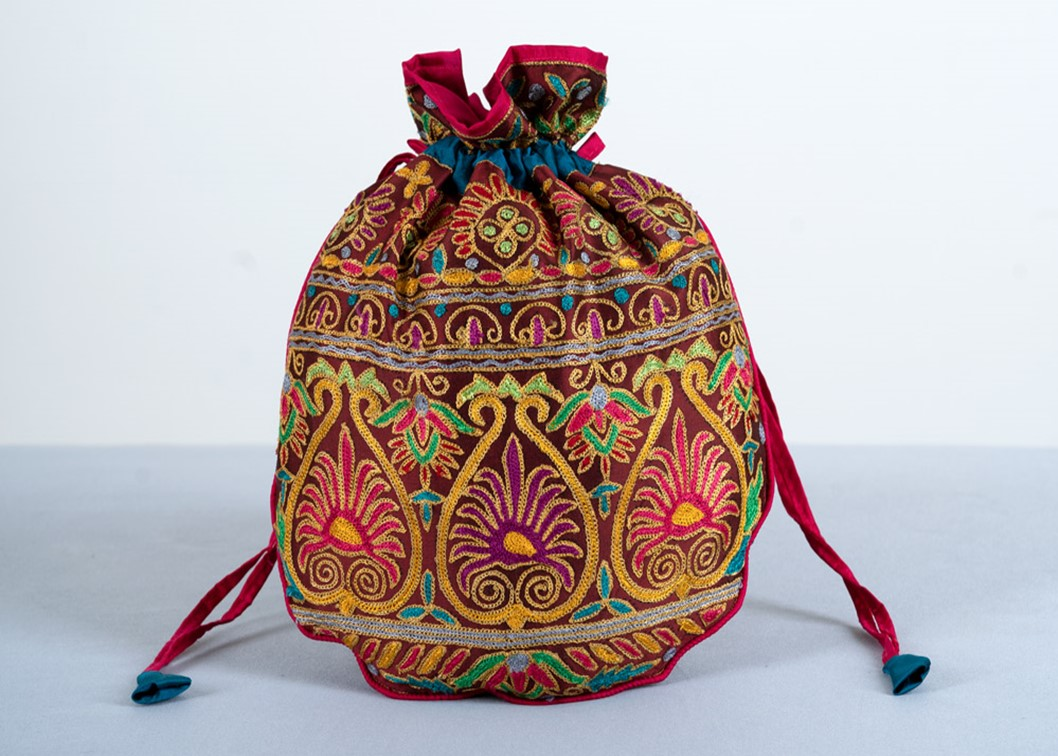
Potli bags are traditional Indian pouches or purses that are typically made from fabric and often embellished with embroidery, beadwork, sequins, or other decorative elements. They have a long history in Indian culture and are used for various purposes, ranging from fashion accessories to ceremonial items. Potli bags are typically cylindrical or pouch-shaped with a drawstring closure at the top. The drawstring allows the bag to be securely closed and carried, resembling a small bundle or pouch.
CRAFTING THE POTLI; AN ART
- Designing and fabric selection
- Pattern making
- Cutting
- Sewing/Stitching
- Assembly
- Finishing
- Quality check
- Packaging
MAKING OF STOLE
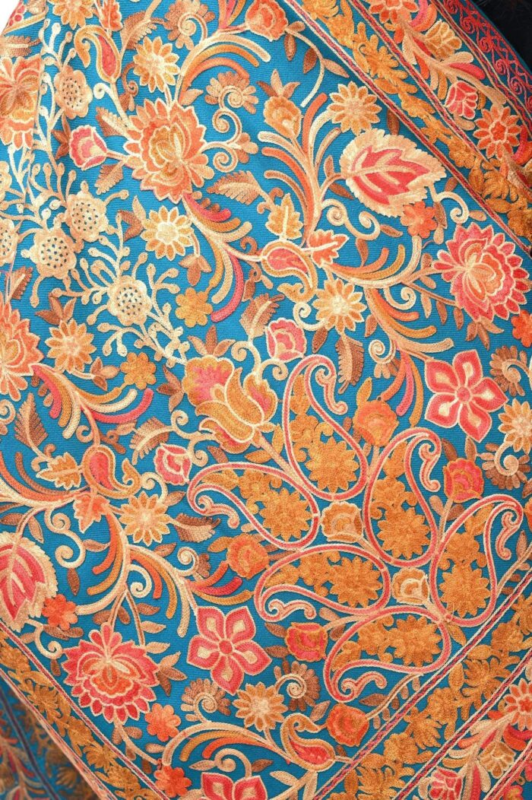
From the time of the Stone Age, Kashmir shows evidence of civilization at sites such as Burzahom, along with pottery and other crafts, highlighting the presence of art in the valley from the beginning of civilizationCulturally, the region continued to bloom from the ancient to the medieval period, when seminal works such as the Natayashastra (10th to 12th century), Rajatarangini, and architecture of different religions were constructed. Patronization of the handmade arts and crafts of Kashmir came from the royal families of Kashmir and the nobility, who knew how to stay royally fashionable even in the most hostile terrains.
MAKING PROCESS OF STOLE
- Wool sourcing
- Spinning
- Dyeing
- Weaving
- Embroidery
- Finishing
- Quality control
MAKING OF BAG
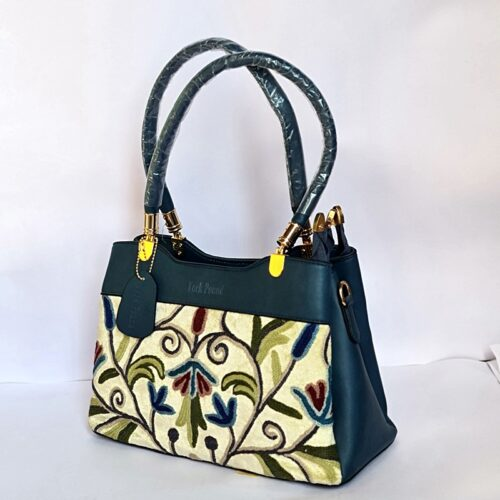
Bags for women come in a diverse array of styles, designs and functions to suit various needs and preferences. Al-Basir provides a variety of bags for our valuable customers including handbags, tote bags, crossbody bags, satchels, clutches, hobo bags and many more which serve different purposes and style preferences. Artisans bring their creativity and expertise to the process of making bags, infusing each piece with unique character and craftsmanship. By leveraging their creativity, skill, and passion for their craft, artisans create bags that are not just functional accessories but also works of art that inspire and delight customers with their beauty and craftsmanship.
PROCESS OF MAKING BAGS
- Design Innovation
- Material section
- Attention to detail
- Customization
- Embellishment and techniques
- Hand crafting techniques
- Experimentation
- Sustainabality
- Quality control
- Packaging
- Distribution
Please call our Customer Care for any query. (9am to 6pm) +91 9463 777 888 or write @ info@albasir.in.