KAFTAN
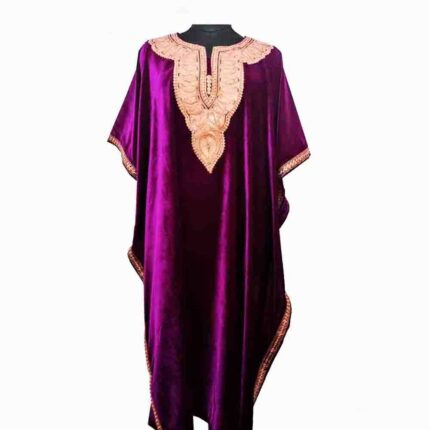
Kaftan or Caftan is a single piece dress which can be worn as a shirt or kurti or a nightdress. The only difference is its length. Kaftan requires the entire width of cloth and larger the width, longer will be the length of the sleeves. Stitching is done only at the neck, sides and near the ankles. Caftans are usually stitched with cotton, satin, nylon or silk fabrics and usually have embroidery or a print design near the neck.
PROCESS OF MAKING KAFTAN
- PREPARE YOUR PATTERN
- CUT FABRIC
- SEW SHOULDERS
- SECURE SLEEVES (OPTIONAL)
- SEW SIDE SEAMS
- COMPLETE THE HEMLINE AND NECKLINE
- ADD EMBELLISHMENTS AS NEEDED (OPTIONAL)
- PRESS AND ADMIRE
JACKET
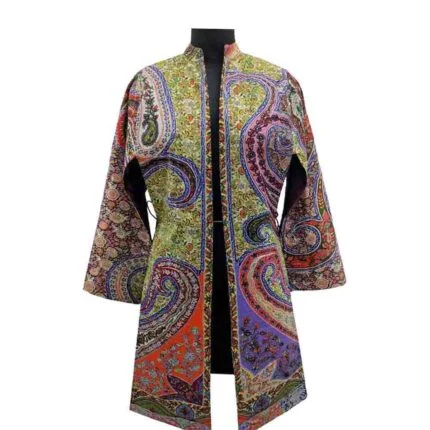
The jacket came to the Museum, along with 10 other pieces, from the collection of Enakshi Bhavnani, author of Decorative Designs and Craftsmanship of India. Kashmir, long associated with the high-quality fabric woven from the wool of cashmere goats, also has its own recognized tradition of embroidery, characterized by delicate designs with motifs following nature—a tradition well represented in this jacket’s exuberant interweaving of flowers. There are different types of jackets like Jacket needle work pashmina, Jacket pashmina ari, Jacket designer woollen, Jacket velvet and many more.
PROCESS OF MAKING PASHMINA JACKETS
- Combing
- Sorting
- Combing again
- Glueing
- Spinning
- These yarns are then made into hanks on a wooden reeler
- Hanks are opened on large wooden stand called thanjoor
- and is then mounted on a wooden spindle called preeh
- Warper
- Purzgar
- Washing
PHIRANS
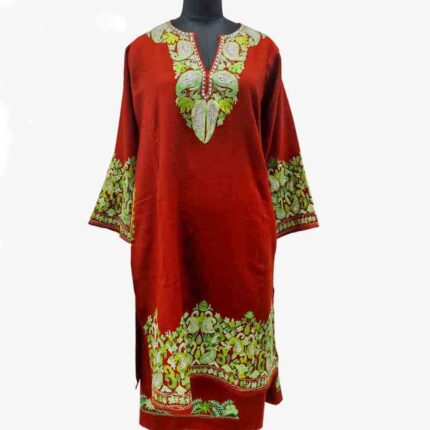
According to some sources, the pheran was introduced by Mughal emperor Akbar when he conquered the valley in 1586. However, according to historian Prithivi Nath Kaul Bamzai, with the arrival of Sufi saints and Muslim theologians from Persia and Central Asia, Kashmiris adopted their long robes and round turbans. The traditinal kashmiri phirans a long, a loose-fitting garment, serves not only as distinctive piece of clothing but aslo as a symbol of the rich culture of kashmiri valley worn by both men and women, the phiran is a garment deeply embedded in the history and lifestyle of the people of kashmir. we have different types of phirans such as woollen phirans, pashmina phirans, velvet phirans etc.
PROCESS OF MAKING PHIRANS
- The first step in making a Pheran is selecting the fabric. Pashmina wool, which is known for its warmth and softness, is the preferred choice for making Pherans. However, other types of wool like Shahtoosh and Raffal are also used.
- After selecting the fabric, it is washed and dyed using natural dyes to achieve vibrant colors. The most commonly used colors for Pherans are black, maroon, and shades of blue.
- Once the fabric is dried, it is stretched over a wooden frame, and the artisan meticulously begins the embroidery work.
- The embroidery on a Pheran is done using a fine needle and silk thread.
- The artisan carefully creates intricate patterns and designs on the fabric, often taking inspiration from nature and Kashmiri motifs.
- It can take several days or even weeks to complete the embroidery depending on the complexity of the design.
- Once the embroidery is finished, the fabric is carefully cut and stitched to create the desired shape and size of the Pheran.
- The final step involves adding finishing touches like buttons, borders, and tassels to enhance the overall look of the attire.
SWEATERS
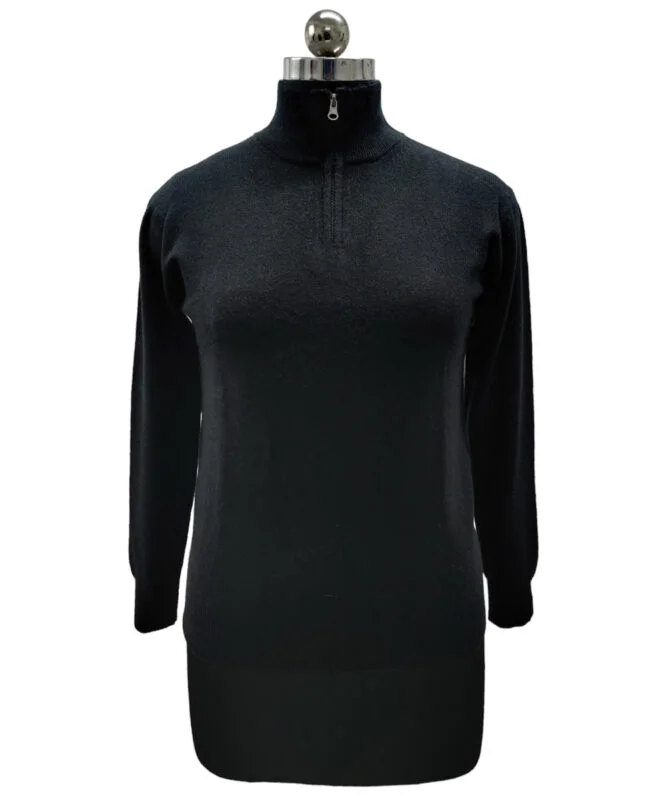
Albasir offers a diverse range of sweaters crafted from premium pashmina fibers, each tailored to meet various style preferences and climate needs. From timeless Crewneck Sweaters exuding classic elegance to versatile V-Neck Sweaters perfect for layering over collared shirts, Albasir presents options to suit every occasion and personal taste. For those seeking convenience and style combined, their collection of Cardigan Sweaters provides effortless sophistication with easy-to-wear open-front designs that can be buttoned or zipped. With meticulous attention to detail and a commitment to quality, Albasir ensures that their sweaters not only offer exceptional warmth and softness but also elevate any wardrobe with their timeless charm and versatility. Sweaters worn by both men and women.
PROCESS OF MAKING SWEATERS
- Firstly let’s take a look at how fabrics are constructed as this impacts their construction into apparel items.
- Wovens and Jerseywear is cut to a pattern which is laid out on flat fabric and cut out into pattern pieces.
- SEWN into clothes using a sewing machine.
- But a sweater is knit to shape on a flat bed machine.
- And the pieces come off the machine already shaped.
- LINKED together using a machine that looks like this, using yarn instead of sewing thread.
- Linking using yarn rather than thread makes the knitwear seams lay flat and gives the seam stretch (which is especially important when pulling ribbed necks over heads!)So, when you’re designing a sweater, you need to think about the yarn, stitches, trims (ribs, etc) and the silhouette and combine all of those things at the same time.
KURTA SETS
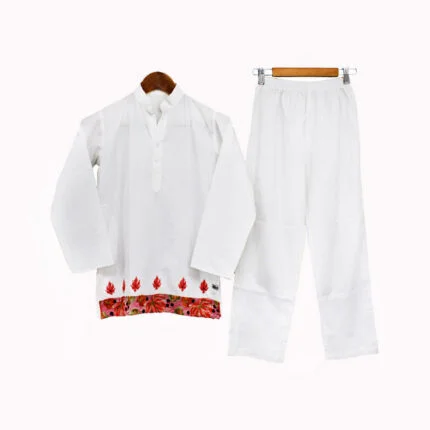
Allow us to introduce our distinguished collection of Kurta Pyjama Sets, a testament to exquisite craftsmanship and unparalleled quality. Handcrafted from premium fabrics including cotton, pashmina, cashmere, woolen, silk, velvet, and a selection of other high-grade materials, our kurta pyjamas epitomize luxury and comfort. Our team of expert designers has curated an exceptional array of designs, showcasing a diverse range of patterns such as Jamawar, Jaal, designer motifs, border patterns, intricate weaves, stripes, khadi, kalamkari, checks, and an array of captivating prints. Within our atelier, we are privileged to house skilled artisans whose mastery extends to ari work, zari embellishments, kalamkari detailing, adornments, and an assortment of intricate techniques. Each garment is meticulously crafted, with meticulous attention paid to color schemes and patterns, resulting in a truly incomparable piece. The creation process for each artwork spans several months, underscoring the dedication and meticulous effort invested in its creation. We invite you to explore our collection and experience the epitome of craftsmanship and elegance in every stitch.
PROCESS OF MAKING KURTS SETS
- Wash the material if needed to prevent shrinking and fading.
- Iron the fabric if you see any wrinkles.
- Grab some paper so you can write down all the measurements you take.
- Use a measuring tape to measure the person’s length.
- Start with a bigger kurta, to allow for adjustments and seams.
- Fold the fabric and cut according to the measurements.
- Sewing the cutting fabric.
- Embroiery or any type of emblishments.
- washing, remove all stain added during the stitching.
- Fusing/ironing.
- pacakaging.
WAIST COATS
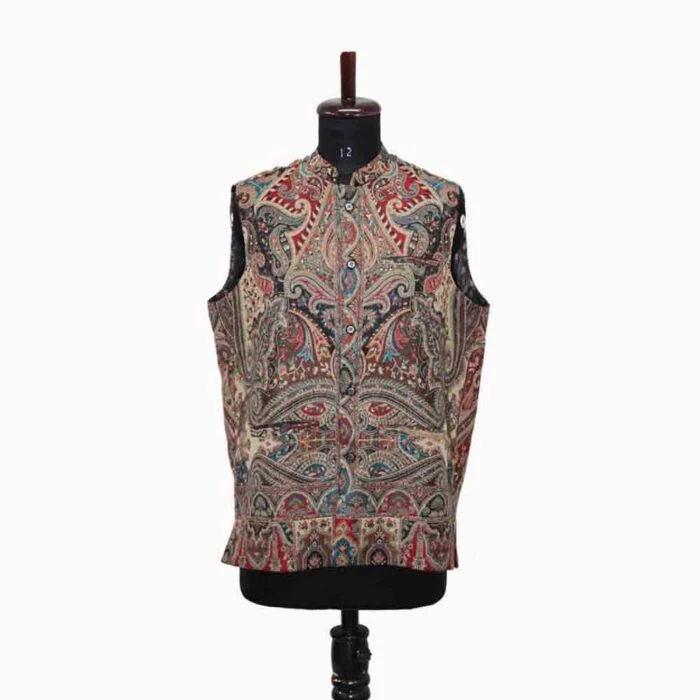
Explore our exquisite collection of Waistcoats, where discerning individuals can indulge in the ultimate array of choices tailored to both men and women. We take immense pride in our curation, offering a diverse selection of waistcoats meticulously crafted from luxurious fabrics, including wool, cotton, silk, velvet, and other premium materials. Within our repertoire, one finds a symphony of designs, each a testament to the artistry of our master designers. From the intricate elegance of Kani weaves to the timeless allure of stripes, khadi patterns, checks, and beyond, our collection embodies unparalleled creativity. At the heart of our craftsmanship lies a dedication to artisanal excellence. Our team of talented craftsmen, skilled in various techniques such as needlework, aari work, appliqué, zari embroidery, pashmina, Swarovski embellishments, and now, the enchanting art of Kalamkari handprints, imbue each waistcoat with an exquisite touch of tradition and innovation. Every waistcoat within our collection is a masterpiece in its own right, meticulously designed with meticulous attention to detail. From the careful selection of colors to the harmonious interplay of patterns, each piece exudes a timeless elegance that transcends fleeting trends. The creation of each waistcoat is a labor of love, requiring dedicated months of craftsmanship to ensure the highest standards of quality and craftsmanship. At our company, we invite you to experience the artistry, luxury, and sophistication of our waistcoat collection, where every garment tells a story of impeccable craftsmanship and enduring style.
PROCESS OF MAKING WAIST COATS
- First, lay your shirt out. trace around the back section and 1 front section, ignoring the collar and sleeve. I tend to use wrapping paper to draw around (then I can use masking tape to join the pieces together to check I have things where I want them).
- From the pieces you have drawn around, you want the back piece to stop higher than a shirt, so measure from the base of the neck to the length you want – probably just passed the trouser waistband, and trim your paper accordingly.
- At the front, waistcoats I think look best with the more traditional pointed shape at the bottom, so start the same length as your shortened back piece then curve down into a point then diagonally up to the centre line. Change the neck line into a V shape then add a seam allowance all the way around (I added 1/4 inch).
- Cut out 2 front pieces and 1 back piece
- add interfacing if you’d prefer a stiffer centre, or interfacing just to the buttonhole area to reinforce it there and help the button holes look sharp and keep their shape.
- To start off, I first attached the shoulder pieces of the front and back pattern pieces. However, if you prefer,you can skip this step, and hand sew the shoulder seams instead Of turning under the arm holes.
- If you are adding an extra layer, just attach it to the back of one of your fabrics. You may want to stitch them together first to stop the pieces moving around so they sew as if they are a single piece of fabric. Since it’s reversible, it doesn’t matter which fabric you add it to the back of.
- Next, I joined the 2 waistcoat pieces together. I placed them right sides together and pinned the edges. I sewed all the way around except the arm holes and a small gap at the bottom at the back for turning it right side out again.
- I tucked the raw edges under for the arm holes, held it in place with lots of pins then top stitched around. I started and finished at the armpit so that any slight alignment issues would be hidden under there.
- Lastly was the buttons. When doing buttons I prefer to put in the button holes first then sew the buttons after as I find it easier to adjust the positioning if I haven’t quite got the spacing as equal as I thought. I added buttonholes as normal on one side of the waistcoat.
PLAZZOS
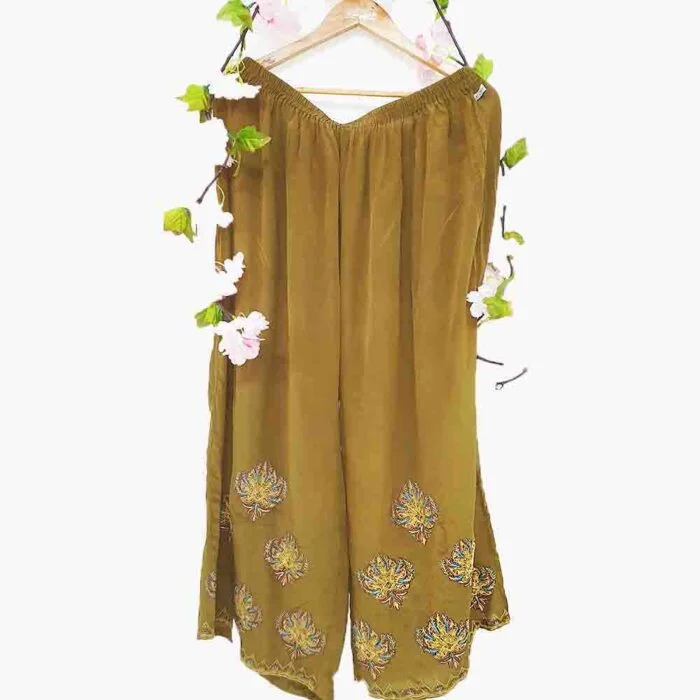
Indulge in the opulence of our diverse palazzo collection, meticulously curated to cater to your discerning taste. Explore a plethora of luxurious fabrics that adorn our palazzo, including the sumptuous allure of pashmina, the delicate grace of net, the timeless elegance of silk, the plush comfort of velvet, and more. Our master designers craft unmatched designs including jamawar, Jaal, designer, border, motifs, designer weave, kani, reversible, stripes, khadi, kalamkari, checks, and other attractive patterns. Skilled artisans in our company excel in various techniques such as needlework, ari work, applique, zari, kalamkari, Swarovski work, lace, and more. presenting a mesmerizing array of designs. From the intricate beauty of jamawar to the delicate allure of Jaal, from the contemporary charm of designer patterns to the traditional richness of borders and motifs, from the elaborate craftsmanship of designer weaves to the classic appeal of stripes and checks, our collection encompasses a myriad of styles to suit every preference. At the heart of our artisanal excellence lie skilled craftsmen who specialize in an array of techniques, elevating each palazzo to a work of art. From the intricate precision of needlework to the exquisite detailing of ari work, from the timeless elegance of appliqué to the shimmering beauty of zari, from the captivating allure of kalamkari to the dazzling embellishments of Swarovski work, and the delicate intricacy of lace, our artisans imbue every piece with unparalleled beauty and finesse.
PROCESS OF MAKING PLAZZO
- Fold the Fabric in Half : Fold your Fabric in half length wise. You should have a two folds on one side and a fold and two raw edges on the other.
- Cut the top of the Fabric : Cut 4″ from the top of the fabric to use as the waist band. Set aside.
- Mark the Measurements : Measure down 12″ from the raw edge side and make a mark. Measure across 3 1/2″ toward the center and draw a line. Take a ruler and draw a line from the short line to the top. Draw a curve from the short line to the long line you just drew creating the crotch of the palazzo pants.
- Cut out the Crotch Area of the Palazzo Pants : Cut along the long line and the curve to create the crotch area. Cut along the long folded edge that is on the raw edge side of the pants.
- Open the Pants and Stitch the Inner Seam : Open the pants. Take each piece separately and stitch the inner straight seam using a 1/2″ seam allowance. The crotch remain unstitched. Turn one leg right sides out.
- Stitch the Crotch : Place the leg that is right sides out inside the leg that is wrong side out so that they are right sides together. Match the crotches. Stitch the crotches together. Turn right sides out.
- Stitch the Waistband : Measure the waistband so that it is the same as the waistband on the pants. Stitch the short ends together. Place the waistband right sides together with the top of the pants and stitch it to the pants. Turn the waistband to the wrong side. Turn under the raw edges and stitch the waistband to the pants leaving an opening to insert the elastic. Using a safety pin insert there elastic into the opening you left in the waistband.
- Hem the Palazzo Pants : Hem the pants to the length that you want them. You are now finished with your palazzo pants without a pattern.
PONCHO
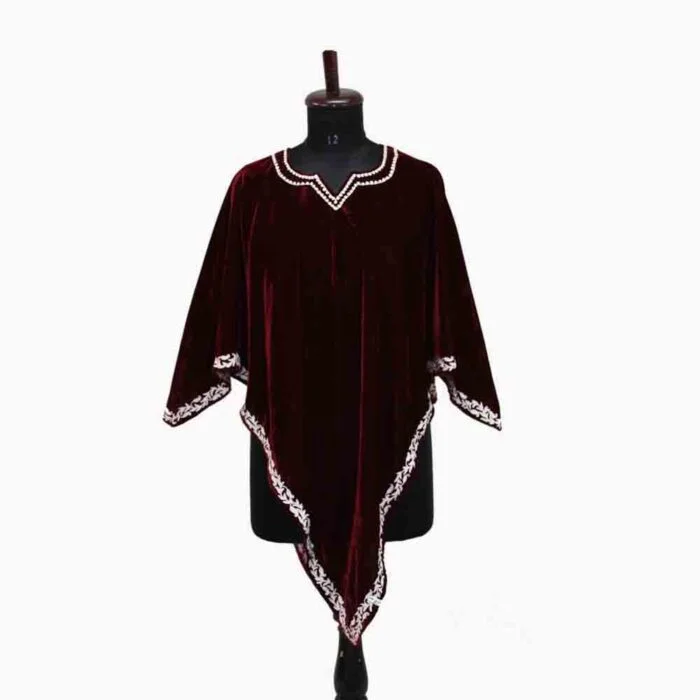
Indulge in the exquisite allure of our stunning collection of cashmere ponchos, meticulously crafted to perfection. Each piece showcases the impeccable artistry of intricate designs such as jaal, jamawar, borders, motifs, and designer patterns, among others. We pride ourselves on using only the finest fabrics, including pashmina, silk, wool, georgette, net, cashmere, velvet, and more, ensuring both opulence and comfort. Our team of skilled artisans employs a diverse range of techniques, from ari embroidery to sozni, appliqué, needlework, and other artistic methods, to weave captivating designs into every fabric. The result, Ponchos that exude timeless allure and sophistication, epitomizing our modern collection’s versatility and style. Whether paired with pants, jeggings, tights, or salwar, our ponchos effortlessly elevate any ensemble, making a bold statement while exuding effortless elegance. Embrace the epitome of luxury and style with our enchanting cashmere ponchos, a true testament to exquisite craftsmanship and enduring beauty. And that’s not all – discover our exclusive additions of kalamkari and kani weave ponchos, adding even more diversity and charm to our already exquisite collection.
PROCESS OF MAKING PONCHO
- Grab a blanket or square-shaped piece of fabric of suitable size. Ponchos can be nearly any size – they can range from waist-length or higher to floor-length. However, most ponchos should hang down to about wrist-level when your hands are at your sides (and slightly lower on the front and back of your body).
- Fold the fabric in half. Next, fold your fabric in half so that the edges meet. Lay your folded fabric flat on a table or a clean, open spot on the floor.
- Cut a hole for your head. Carefully use a pair of scissors or a fabric knife to cut a slit along the folded edge of the fabric. The slit should be centered along the folded edge – you will probably want to use a tape measure to find the exact center of the fabric’s length before cutting to ensure the poncho sits evenly on your shoulders.
- Optionally, hem the seams around the head hole to prevent fraying and curling. At this point, your poncho is essentially “done” – it can be worn and will work as intended. However, if you have the time (and care to do so), you may want to spend a little extra effort making your poncho more durable. The “rough”, unprotected edge created by cutting your head hole is vulnerable to wear and tear – over time, you may notice it begin to fray. To prevent this, sew a hem around the edge of the head hole to strengthen the material and extend your new garment’s life.
- Optionally, add flair! When it comes to making your poncho more functional or eye-catching, you have a variety of options.
TUNIC
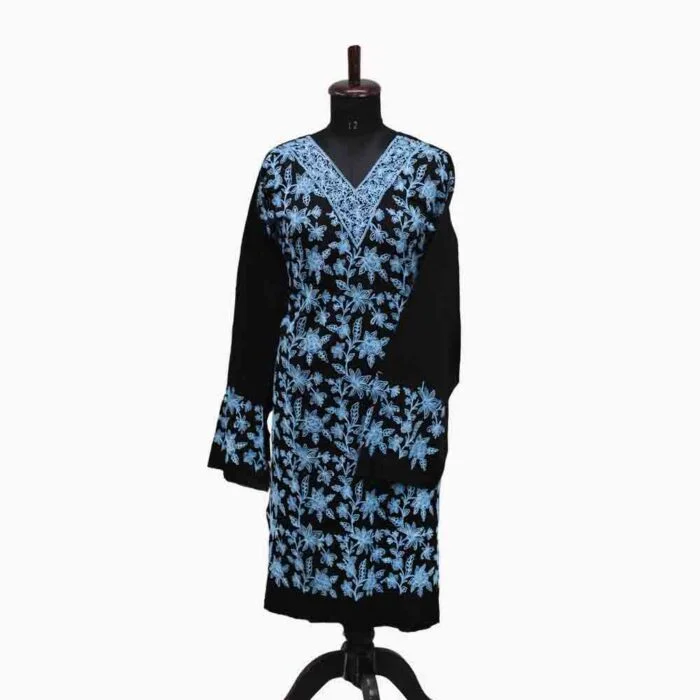
Introducing our exquisite tunic collection, meticulously crafted from the most luxurious fabrics and conceptualized by our esteemed master designers. Each piece is a testament to opulence, featuring a rich array of materials such as chiffon, pashmina, crepe, woolen, cotton, Chinon, net, silk, velvet, and more, sourced for their unparalleled quality. Our designs are a fusion of creativity and sophistication, offering a diverse range including jamawar, Jaal, designer motifs, border detailing, stripes, khadi, checks, and an array of captivating patterns to suit every taste. Crafted by skilled artisans renowned for their expertise in needlework, ari work, applique, zari embellishments, Swarovski detailing, lace accents, and other intricate techniques, each tunic exudes an aura of elegance and comfort. We invite you to indulge in the unparalleled luxury of our tunics, confident that you will find in them the perfect embodiment of style and refinement. Explore our collection today and elevate your wardrobe with our signature pieces. Additionally, discover our exclusive offerings, including special kani weave, kalamkari printed tunics, handmade pashmina tunics, handloom pashmina tunics, and power loom creations, each adding a distinctive charm to your ensemble.
PROCESS OF MAKING TUNIC
- Place the fabric length on a table or the floor. To make the cut edges meet, fold the fabric in half across the center. Further smooth out any folds or wrinkles. The fabric should now be folded lengthwise so that the selvedges (clean edges) meet. The fabric should be folded into quarters neatly. The shorter of the two folded edges will be referred to as the “Top” edge, while the longer fold will be referred to as the “Centre.”
- Using chalk and a measuring tape, make some marks on the cloth.
- You may also make the tunic slightly narrower at the wrists or flare out at the elbows.
- Make a curved hemline by curving the line. Smooth out the side seam so the waist isn’t at a sharp angle. A continuous curved side seam should be present. Cut along the hemline and side seams of the tunic, running all the way to the wrist. If you need to cut out an extra sleeve piece from the leftover fabric, now is the time to do so.
- Both the facing and the neckline should be open. The facing should be pinned to the inside of the tunic if you want it to end up on the outside. The neck holes should be the same.
- Sew the facing down in a neat manner. You can also sew down the facing by hand. Pin and sew the sleeve extensions in place if possible.
- Fold the tunic at the shoulder seams keeping right sides together. Try it on and pin along the side and underarm seams to make sure it matches.
NIGHT GOWN/DRESSES
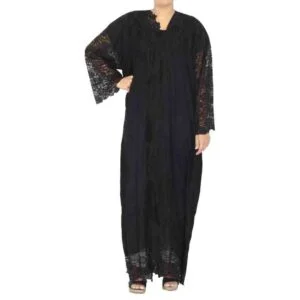
Our nightwear collection is a testament to opulence, boasting an exquisite array of luxurious fabrics that include the likes of pashmina, cashmere, woolen, cotton, chinon, net, silk, velvet, and a selection of other premium materials. Within this tapestry of elegance, our master designers weave their magic, fashioning exceptional designs that span the spectrum from traditional to contemporary. From the intricate motifs of jamawar to the delicate Jaal patterns, from designer weaves to striking borders, and from reversible styles to bold stripes and checks, each piece in our collection is a masterpiece in its own right, designed to captivate and enchant. At the heart of our craftsmanship are our skilled artisans, whose expertise in various intricate techniques knows no bounds. With a deft hand, they employ needlework, ari work, appliqué, zari embellishments, kalamkari artistry, Swarovski detailing, lacework, and a plethora of other techniques to breathe life into our designs. Each product undergoes a meticulous design process, where every hue, every stitch, and every detail is carefully considered, resulting in unparalleled pieces of wearable artistry that are as unique as they are timeless. It is a labor of love that spans months, culminating in nightwear that transcends mere garments to become cherished heirlooms, treasured for generations to come.
PROCESS OF MAKING GOWN/DRESSES
- The first step of making gown/dresses is selecting fabric.
- After selecting the fabric, it is washed.
- Once the fabric is dried, then spread onto the table.
- Marking all the measurements on the fabric.
- sew the garment.
- Embellishment.
- The artisan carefully creates intricate patterns and designson the fabric.
- the final step involves adding finishing touches like buttons, boarders, and tessel to enhance the overall look of the attire.
DRESSES
Co-ord derives from its name coordinates, and its sartorial aspect means a matching set top and bottom. In short, coordinate sets are matching outfits that consist of a top and bottom, which are designed to be worn together to create a cohesive and coordinated appearance. In the 1920s, Coco Chanel made a comfy jersey cardigan and skirt set. In the 1950s and 60s, there was a burst of colorful co-ord sets with bold prints. A co-ord set is a set of multiple pieces of clothing . Top and bottom wear designed and paired in such a manner that they are made from the same or similar material and fabric to give a uniform look.
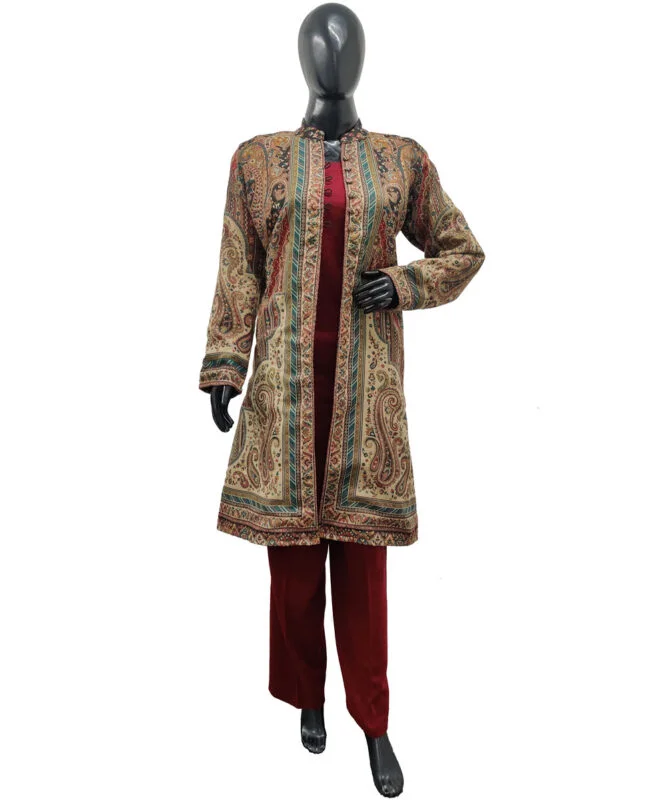
The co ord sets for women are designed in a variety of styles to create very fashionable looks.
PROCESS OF MAKING CO-ORD SETS
- Fabric: Fine wool or Pashmina.
- Design: Inspired by Kashmiri motifs like paisleys and chinar leaves.
- Embroidery: Intricate hand-embroidery using Aari, Sozni, or Tilla techniques.
- Weaving: Hand-woven on traditional looms for detail and quality.
- Dyeing: Natural dyes for vibrant colors.
- Assembly: Meticulously stitched by skilled artisans.
- Final Touches: Inspection for quality and fit.
- Finishing: Blocking or pressing for appearance.
- Quality Check: Rigorous checks before packaging.
Please call our Customer Care for any query. (9am to 6pm) +91 9463 777 888 or write @ info@albasir.in.